Anti-corrosion performance test of non-electrolytic zinc sheet coating on socket countersunk head cap screw
After many screw fasteners are made, the screw fasteners are surface treated to increase the characteristics of a certain aspect. After surface treatment of the socket countersunk head cap screw, we also need to test whether the surface’s anti-corrosion performance / wear resistance can not meet our needs.
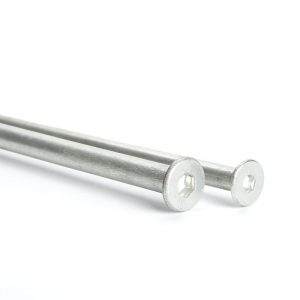
When the anti-corrosion performance test of the non-electrolytic zinc sheet coating of the socket countersunk head cap screw is carried out, the quality of the zinc coating layer is evaluated according to the neutral salt spray test specified in GB/T 10125. This test should be performed on parts that are in delivery. The performance of the modified test is independent of the corrosion resistance of the socket countersunk head cap screw in their specific service environment.
Neutral Salt Spray Test Time
μm
Test time/h |
Minimum local zinc coating thickness (specified by the purchaser when required) |
Zinc coated sheet and passivated by chromate/(flZnyc) |
Zinc-coated sheet is not passivated by chromate/(flZnnc) |
240 |
4 |
6 |
480 |
5 |
8 |
720 |
8 |
10 |
960 |
9 |
12 |
Note: If the purchaser specifies the average quality of the zinc coating, the thickness can be converted as follows:
- Zinc-coated layer and passivated by chromate: 4.5 equivalent to 1μm thickness
- The zinc coated layer is not passivated by chromate: 3.8 is equivalent to 1 μm thickness
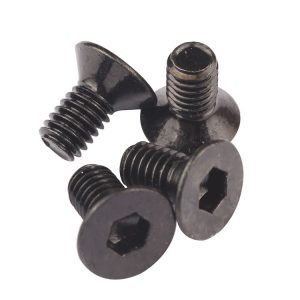
If you want to customized socket countersunk head cap screw, please send an email: annie.li@szsst88.com